Marcatura laser di codici 2D (Data Matrix / Codici QR / Codici a barre)
Le continue richieste di prodotti sempre più piccoli e sottili e di una tracciabilità più dettagliata portano a dover inserire sui prodotti fabbricati un maggior numero di informazioni in uno spazio limitato.
Un codice 2D può contenere da decine a centinaia di volte le informazioni di un codice a barre. Grazie a questa densità elevata di dati, un codice 2D può contenere la stessa quantità di informazioni di un codice a barre in appena 1/30 delle sue dimensioni. Queste importanti caratteristiche hanno favorito la crescita delle applicazioni in vari campi.
- Esempi di applicazioni di codici 2D
- Classificazione dei codici 2D
- Funzione di marcatura 3D
- Profondità della messa a fuoco
- Pattern di marcatura
Esempi di applicazioni di codici 2D
L'uso di codici 2D semplifica la gestione, migliora la precisione e riduce le ore di lavoro. Negli ultimi anni, la tracciabilità dettagliata viene richiesta non solo per i prodotti finiti ma anche per le singole parti. Il numero di codici 2D marcati direttamente con un marcatore laser è in crescita. Di conseguenza, per garantire una lettura stabile del codice 2D è richiesta una marcatura di alta qualità.
Industria dei dispositivi elettronici
- Telecamera
-
- I codici 2D consentono il controllo seriale di parti minuscole con uno spazio di marcatura limitato. Per tenere il passo con un controllo di qualità sempre più rigoroso serve quindi flessibilità.
- Pacemaker
-
- Per gestire la tracciabilità, nei codici 2D si può memorizzare lo storico di produzione e di ispezione. Leggendo il codice è possibile controllare rapidamente le informazioni di questo storico.
Industria automobilistica
- Blocco cilindri
-
- Su ogni prodotto viene marcato un numero di serie tramite codice 2D, che viene letto nei processi successivi per dare istruzioni di lavoro ai robot.
- Iniezione
-
- I dati storici, inclusa la data di produzione e le informazioni sulla linea, vengono marcati su ogni prodotto in un codice 2D e utilizzati per la gestione della tracciabilità.
Classificazione dei codici 2D
Per garantire una lettura stabile, è importante che la marcatura possa essere letta facilmente dai lettori di codici 2D. Per la lettura di questi codici esistono alcuni standard. La facilità di lettura può essere espressa in gradi. In genere, per valutare la marcatura diretta dei prodotti realizzata con marcatori laser viene usato uno standard chiamato ISO/IEC TR 29158 (AIM DPM-1-2006)*. Questo standard specifica i seguenti criteri per la valutazione dei gradi di lettura.
Si tratta di uno standard internazionale per la valutazione della qualità della marcatura diretta di codici 2D sulle parti.
- 1Valutazione complessiva (Tutti)
-
La valutazione complessiva è determinata come il grado più basso tra i criteri da 2 a 11. Il risultato è espresso con una lettera da A a D o F, dove A è il grado più alto (stabilità di lettura).
- 2Decodifica riuscita/non riuscita (DEC)
-
Valutazione della decodifica (lettura): riuscita o non riuscita
- 3Contrasto tra celle (CC)
- Differenza nei valori di intensità della luce media tra celle chiare e celle scure
- 4Modulazione delle celle (CM)
- Valutazione del grado di variazione della luminosità delle celle
- 5Margine di riflettanza (RM)
Valutazione del grado di variazione della luminosità della cella con il bianco e il nero della corretta cella considerata
- 6Danni al pattern fisso (FPD)
-
Entità dei danni al pattern fisso (vedere la figura sotto)
- 7Danni alle informazioni sul formato (FID)
-
Entità dei danni alle informazioni sul formato di un codice QR (vedere la figura sotto)
- 8Danni alle informazioni sulla versione (VID)
-
Entità dei danni alle informazioni sulla versione di un codice QR (Modello 2 versione 7 e successive)
- 9Non uniformità assiale (AN)
-
Grado di distorsione delle dimensioni verticali e orizzontali di un codice
- 10Non uniformità della griglia (GN)
-
Valutazione del massimo disallineamento tra le posizioni delle celle
- 11Correzione inutilizzata degli errori (UEC)
-
Percentuale delle correzioni degli errori che non vengono utilizzate per la decodifica
Nella marcatura diretta delle parti su superfici metalliche, CC, CM, RM e FPD sono spesso inferiori quando non è possibile ottenere il contrasto. L'obiettivo per garantire una marcatura leggibile è quello di impedire che questi valori scendano. Negli ultimi anni viene richiesto principalmente il grado C o superiore. È auspicabile raggiungere gradi più alti subito dopo la marcatura.
Funzione di marcatura 3D
Per la valutazione dei codici 2D è importante la differenza di contrasto tra le celle bianche e nere. Un marcatore laser produce colori diversi cambiando le condizioni di marcatura tra quella bianca e quella nera.
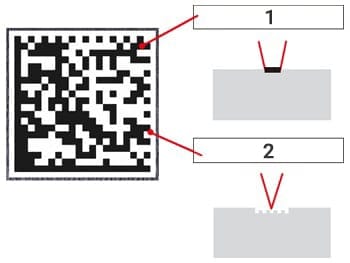
- 1. Marcatura nera (ossidazione)
- Quando il raggio laser viene applicato al target di marcatura, la messa a fuoco viene spostata affinché venga condotto solo il calore. L'applicazione del calore senza incidere il target forma una pellicola di ossido sulla superficie. Questa pellicola appare nera e rappresenta la marcatura.
- 2. Marcatura bianca tramite rasatura superficiale
- Il raggio laser viene applicato al target di marcatura nel punto focale. La superficie metallica viene leggermente asportata per creare una superficie irregolare. Ciò causa la riflessione irregolare della luce che determina una marcatura di aspetto bianco.
- Dimensioni variabili dello spot del fascio
-
- Dimensione spot alle coordinate impostate
La marcatura del codice 2D crea un contrasto tra il bianco e il nero tramite la rasatura superficiale e l'ossidazione. La chiave sta nell'usare la marcatura bianca con una messa a fuoco corretta e la marcatura nera con una messa a fuoco sfocata. Le dimensioni variabili dello spot del fascio della funzione di marcatura 3D rappresentano un approccio efficace.
Per la marcatura del codice 2D il contrasto è importante. La correzione 3D è un metodo efficace per mantenere la messa a fuoco su tutta l'area.
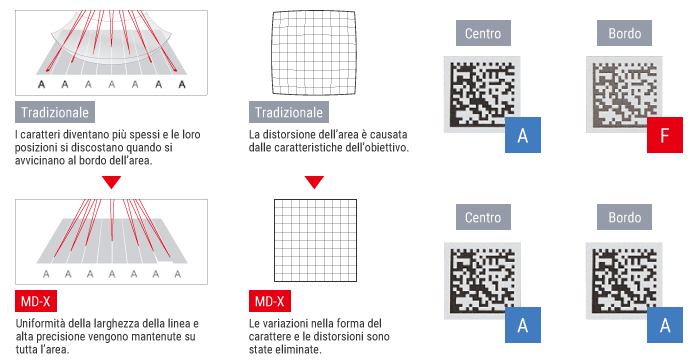
È possibile ottenere facilmente una marcatura ideale al centro dell'area di marcatura. Senza la correzione della funzione di marcatura 3D, potrebbe essere difficile ottenere su tutta l'area di marcatura un contrasto evidente tra bianco e nero, cosa che porterebbe a un declassamento del grado di leggibilità del codice 2D.
Profondità della messa a fuoco
Un raggio laser ha una certa profondità di messa a fuoco. Quando la messa a fuoco devia, la qualità della marcatura si deteriora e questo influisce anche sulla lettura del codice 2D.
Il grado del codice 2D cambia in base alle distanze focali
Man mano che la distanza focale si allontana dalla posizione di riferimento, la marcatura sbiadisce e il contrasto si riduce, determinando un grado inferiore. Sebbene la profondità di messa a fuoco consentita vari a seconda del metodo di oscillazione laser, occorre impedire la deviazione della messa a fuoco mantenendo una distanza focale costante tra il target e il marcatore laser o utilizzando un sensore di spostamento.
- Marcatore laser a fibra KEYENCE
-
- Marcatore laser YVO4 KEYENCE
-
Metodo di oscillazione laser e profondità di messa a fuoco
Confronto della distribuzione della potenza del fascio
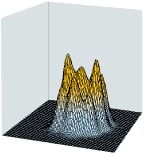
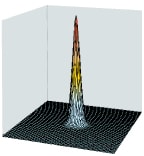
(metodo a pompaggio finale)
La figura a destra mostra un confronto della qualità di marcatura di un laser YVO4 e di uno a fibra. Quello YVO4 è un laser con una potenza di picco elevata e un impulso breve. Ciò consente al laser di irradiare in poco tempo le parti con una forza ideale e un'alta densità di energia. Anche quando la messa a fuoco devia a causa del movimento dei target o della tolleranza del prodotto, la sua qualità di marcatura è stabile rispetto ai tipi a fibra. Per i casi in cui la marcatura è influenzata da un angolo incidente come sul bordo dell'area di marcatura, un laser YVO4 produce una qualità di marcatura stabile senza sbiadimento.
Funzione di messa a fuoco automatica
Meccanismo della funzione di messa a fuoco automatica
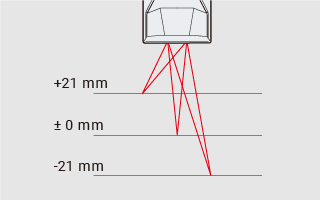
Il marcatore laser della Serie MD-X di KEYENCE ha una telecamera incorporata per regolare automaticamente la messa a fuoco senza la necessità di un dispositivo esterno. Mantiene una qualità di marcatura elevata anche su target che sono tradizionalmente difficili da marcare a causa dell'instabilità della distanza focale. Inoltre, quando cambia il tipo di prodotto, non è più necessario perdere tempo con operazioni di riattrezzaggio, il che riduce enormemente le ore di lavoro, semplifica le strutture e migliora la produttività.
La telecamera incorporata viene utilizzata per monitorare il puntatore laser di misurazione della lunghezza. La distanza focale viene calcolata dalla posizione del puntatore e viene utilizzata per la messa a fuoco automatica. Questa misurazione potrebbe essere instabile a seconda del materiale, della forma o delle condizioni della superficie del target.
Pattern di marcatura
Il marcatore offre diversi tipi di pattern di marcatura del codice 2D per ottenere una marcatura ottimale in base alle varie condizioni. I seguenti esempi illustrano metodi di marcatura ottimali per alcune condizioni specifiche.
Possibile scelta tra vari pattern di marcatura
- 11 tipi di pattern di marcatura
-
- 6 tipi di pattern base
-
Marcatura nitida di codici 2D
Su alcuni target la lettura potrebbe essere instabile a causa dell'influenza delle superfici metalliche satinate. Per migliorare la percentuale di lettura potrebbe essere sufficiente cambiare il pattern di marcatura di basi o codici 2D.
-
Target con superficie metallica con finitura satinata
-
Quando per la marcatura della base viene utilizzato il raster orizzontale, la satinatura rimasta visibile causa una lettura instabile.
-
Quando per la marcatura della base viene utilizzato il raster a linee incrociate, la satinatura diventa invisibile e la lettura è stabile.
Marcatura più rapida di codici 2D
Il volume di produzione potrebbe portare a un tempo limitato per la marcatura. La selezione di un pattern di marcatura ottimale consente tempi di marcatura più brevi e una maggiore produttività.
-
Pattern B - Marcatura standard che marca le celle una ad una da sinistra a destra
- Tempo di marcatura: 637 ms
-
Intero pattern 2 - Pattern efficiente che marca un intero codice 2D in una sola passata
- Tempo di marcatura: 342 ms
Riduzione del 47% rispetto al metodo tradizionale
Il tempo è stato calcolato con un esempio di marcatura DataMatrix di 16×16 con dimensioni delle celle di 0,3 mm. La valutazione di cui sopra rappresenta un caso tipico. Il risultato varia in base al materiale e alle condizioni della superficie del target e della marcatura.
Incisione di codici 2D
Nei casi in cui dopo la marcatura venga eseguita la placcatura o la tempra, potrebbe essere necessaria l'incisione. Vengono forniti pattern di incisione per consentire in breve tempo un'incisione uniforme anche se profonda.
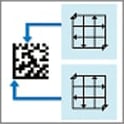
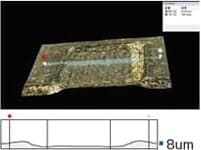
Il raggio laser viene incrociato per ottenere un'incisione uniforme.
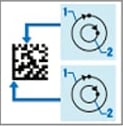
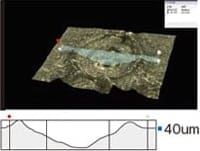
Il target viene inciso in modo concentrico così che il calore accumulato possa eseguire un'incisione più profonda in breve tempo.